Controlling Quality Instead of Just Inspecting It
- Blue Cromos
- Apr 24, 2024
- 3 min read
Updated: Dec 3, 2024
Roy and Rodger wound down after the game. They had played each week since college. Both had since landed jobs as responsible for production and quality in major local industries.

Rodger wasn't happy.
- We've had too high levels of quality issues lately. Too high for comfort. A major portion seems to be caused by simple human error in assembly lines. People just take and mount the wrong part. Parts that might look similar, but with different characteristics. Fittings for a different model or version for example. I suspect we've cut back too much on staff for them to have the time or enthusiasm to put in the needed effort.
Luckily we've caught most of it at the final inspection, but the rework is costly, causes delays and increases pressure even further. Not to mention what it does to our bottom line.
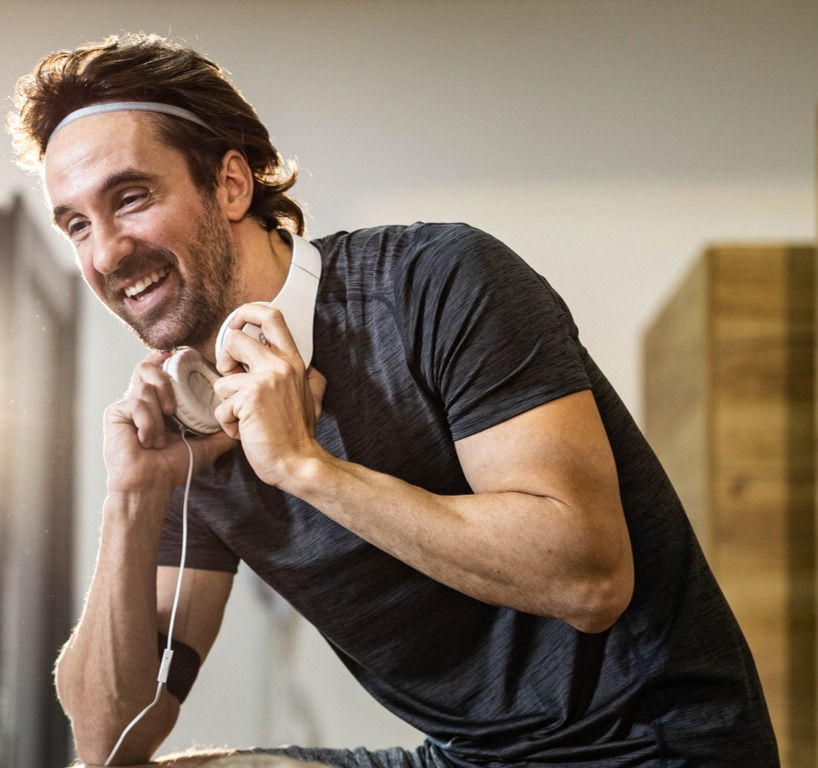
- Been there, fixed that, Roy answered. We've actually shifted much of our quality control from the end of the assembly line to the beginning, and solved much of those issues. We have much better control and consistency now.
- To the beginning? What do you mean? The bewildered Roger wondered.
- Since we introduced automatic component identification, we have cut down human error to insignificance. Roy explained.

- "Automatic component identification"?

Roy explained:
Automatic component identification with the help of isAuthentic, that is. In close cooperation with our component suppliers.
Our specifications to the suppliers include information on exactly which products we use their parts for and where. Models, versions, sizes etc.
When they produce them, they scan each individual component. The system assigns each item an individual ID, supplements the ID with production data like batch number, time stamp etc AND the data we provided in the first place on what we will use it for.
At the start of our assembly lines, we scan the items again. The system compares the scans with the ones from our supplier, fetches the data and compares with our production control system. If there's a mismatch, we nip the problem in the bud, not in the finished product we have wasted time and money to complete.
As a positive side effect, if there turns out to be a quality issue with components, we know exactly which individual component went into which finished product, we can track them and can make a much more limited recall than we did in the old days when we had to scope the recall to be on the safe side.

- Amazing! Rodger shouted. Talk about having control over the quality you produce, not just separating the bad completed stuff from the good as everybody else does. Including us! Both increasing quality and reducing time and efforts wasted on completing faulty products.
That's what I'd call streamlining!
isAuthentic, you said?
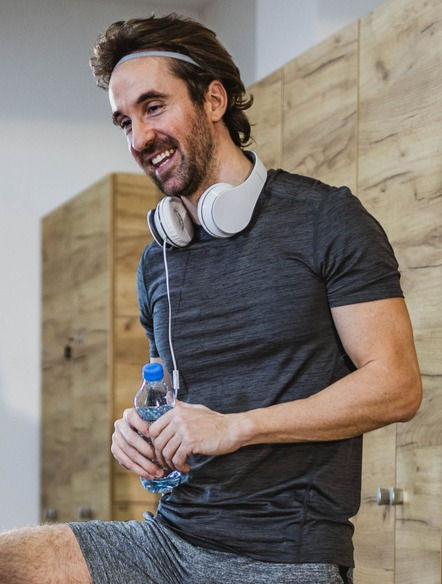
- Yes, isAuthentic by Blue Cromos. Most people aware of isAuthentic probably associate it with authenticating finished products in the field to verify that they are genuine, not counterfeit. We use it for that too, but found out that it could be used this way too, to stop wasting time on producing sub-standard stuff only to weed them out at a later stage.
- I bet. What do the workers think about it, then?

- A bit suspicious to start with, as usually. But now they seem to think of it as an assistant QA helping them to spend their time well and not wasting it on stuff that will build stress later by causing re-work.
- Another win, said Roger.
Images by skynesher on iStock